When it comes to safety, following lifting equipment regulations is of paramount importance. In this article we explore working load limits, the Lifting Operations and Lifting Equipment Regulations (LOLER) and Provision and Use of Work Equipment Regulations (PUWER) legislation and the equipment that is covered under these acts.
What are the Lifting Equipment Regulations, and what do I need to be aware of?
Lifting operations in construction environments can often put people at risk of injury, as well as incurring great costs if they go wrong. To ensure the safety of everyone on site when equipment and materials are being lifted, lifting equipment regulations have been made and enforcements are in place to ensure everyone abides by these rules.
At Conquip, health and safety is paramount, and we believe that everyone involved should be aware of safety regulations and how they may impact them. As a result, we have put together a guide to the most significant regulation requirements relating to lifting – Lifting Operations and Lifting Equipment Regulations 1998 (LOLER), and Provision and Use of Work Equipment Regulations 1998 (PUWER). Both of these regulations came into force in Great Britain on 5 December 1998 (1999 in Northern Ireland), LOLER was created under the Health and Safety at Work Act 1974 (HASWA).
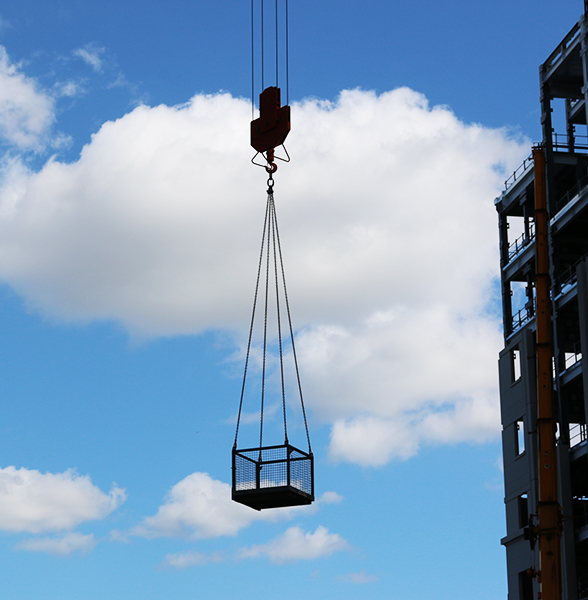
What is LOLER?
Lifting Operations and Lifting Equipment Regulations 1998 (LOLER) requires that all lifting operations involving lifting equipment is properly planned by a competent person, appropriately supervised and carried out in a safe manner. It also requires that all equipment used for lifting is fit for purpose, appropriate for the task and suitably marked, with suitable maintenance recorded and defects reported.
According to LOLER, all workplace lifting equipment should be positioned or installed in such a way as to reduce the risk, as far as reasonably practicable, of the equipment or load striking a person, or of the load drifting, falling freely or being unintentionally released.
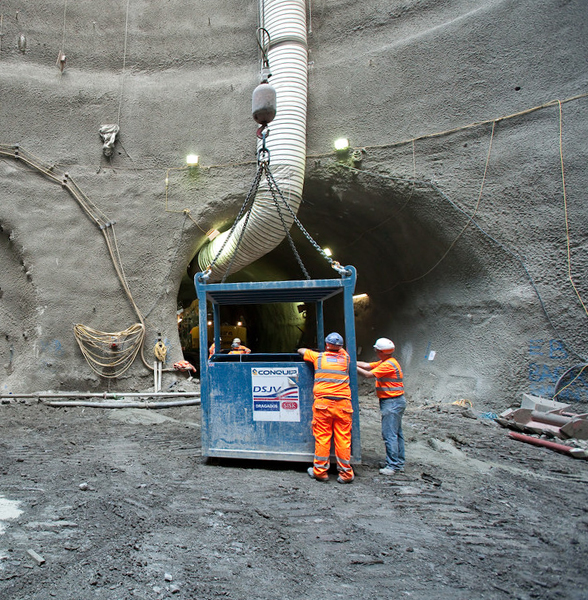
Do I need to be aware of LOLER?
LOWER regulation places the duty on people and companies who own, operate or have control over lifting equipment.
It’s important to remember that that under Section 3 of HASWA, employers and the self-employed have responsibilities, so far as reasonably practicable, for the safety of people they do not employ that may be affected by the employer’s work. Therefore, businesses allowing the public to use lifting equipment, should still be managing the risks of this equipment, and they will generally need to comply to the same stringent standards.
What lifting equipment is covered by LOLER?
LOLER covers any equipment used at work for lifting. Some equipment is not considered as lifting equipment, so is not subject to LOLER’s specific provisions when not at work. This includes items such as escalators, stair lifts and platform lifts for the use of customers within a workplace.
How do I know lifting equipment is fit for purpose?
All equipment must be appropriately marked. Accessories must also be marked to show any characteristics that might affect their safe use. This may include the weight of the parts, where their weight is significant.
Mick Collyer, Head of QHSE at Conquip Engineering Group, advises:
“All lifting equipment, including accessories, must be clearly marked to indicate their ‘Safe Working Loads’ (SWL). SWL, or ‘Working Load Limit’ (WLL) is the maximum load the equipment can safely lift.”
On Conquip products, the WLL is marked in kg on the silver product identification plate. Where the WLL of any equipment or accessory depends on its configuration, the information provided on the WLL must reflect all potential configurations (for example, where the hook of a forklift crane arm can be moved to different positions, the WLL should be shown for each position). In some cases, the information should be kept with the lifting machinery.
At Conquip every piece of lifting equipment, whether for purchase or hire, is inspected by LOLER qualified staff before being dispatched to our customers. Copies of the thorough examination certificates are attached to the products and the original inspection sheet and certificate are kept on file at Conquip.
If you would like a copy of the certification for products supplied to you, simply contact our customer services team, who will be more than happy to arrange an electronic copy of your certificate to be sent to you.
What is PUWER?
PUWER Regulations 1998 replaces PUWER 1992 and deals with any work equipment and machinery being used every day at work. The requirements it enforces aim to keep people safe wherever they may encounter equipment and machinery when it is being used in the workplace. This includes employers, employees, contractors, suppliers and anyone else who may have access to machinery.
PUWER regulations do not refer to equipment that is used by the public, as this comes under the HASWA.
PUWER Regulations covers knowledge, training and experience of the equipment user as well as the equipment’s suitability for the job and examinations and tests.
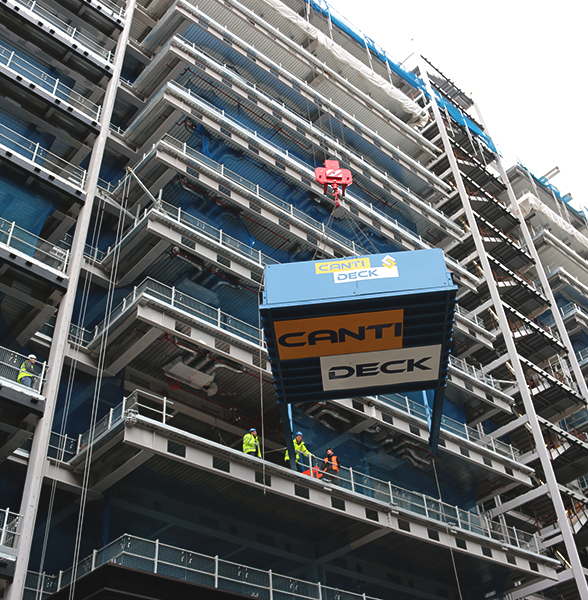
Do I need to be aware of PUWER?
You are obliged to abide by regulations set out by PUWER if you use or control work equipment. The types of people PUWER applies to are employers, self-employed, anyone employed to supervise or manage the use of equipment.
It is the responsibility of the person who has purchased the equipment to ensure it abides to PUWER regulations, it does not present risk to those at work, and is specified, installed and used in the correct manner.
PUWER does not apply to the person or company who has supplied or sold the equipment.
What lifting equipment is covered by PUWER?
PUWER provisions applies to all equipment being used at work, including all lifting equipment. It includes selection, inspection and maintenance of the equipment, as well training involved in using it.
Download Whitepaper
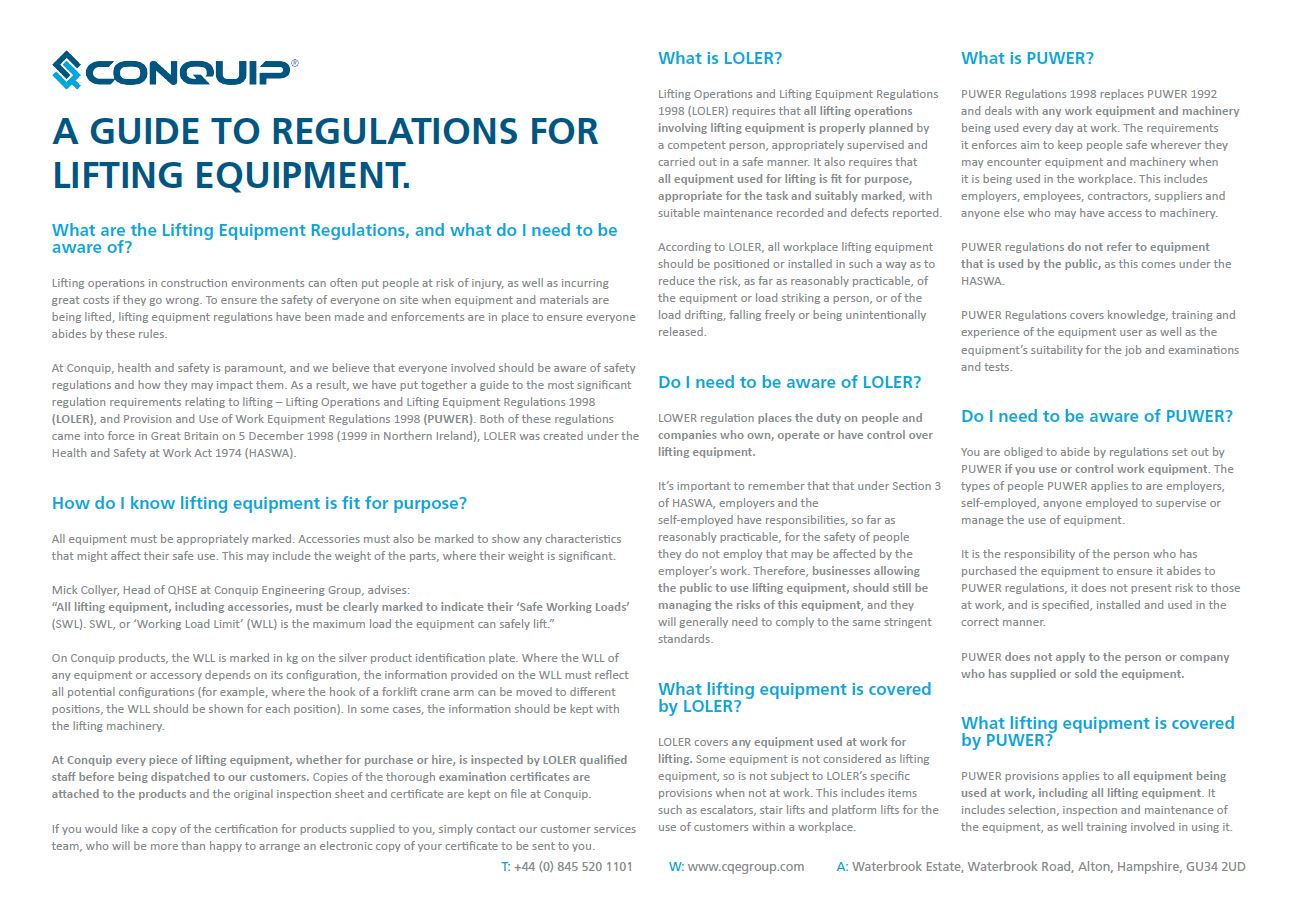